Bosch Siemens Hausgeräte (BSH)End-of-line testing
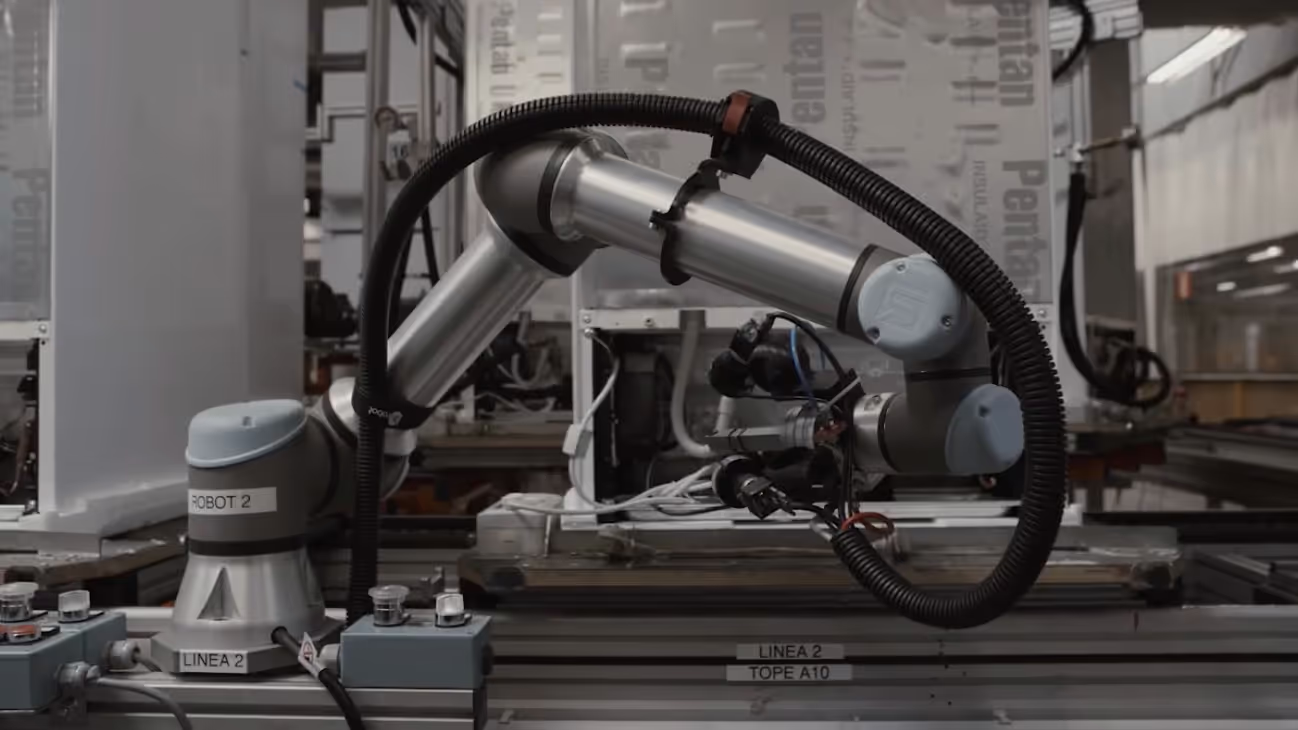
Challenge
Leak testing involves running a sniffer probe along the solder joints of coolant pipes on the back of refrigerators in order to check for leaks. Since each pipe is uniquely positioned and its solder joints vary in shape and color, automating this task was impossible for BSH with traditional automation solutions. For this reason, the task had to be done manually.
Outcome
Thanks to the MIRAI system, BSH has automated the leak testing task. Since the solution was implemented, BSH has lowered ongoing operating costs and reduced maintenance and troubleshooting. Our AI-vision solution is deployed in 24/6 serial production and ensures high quality and absolute process reliability.
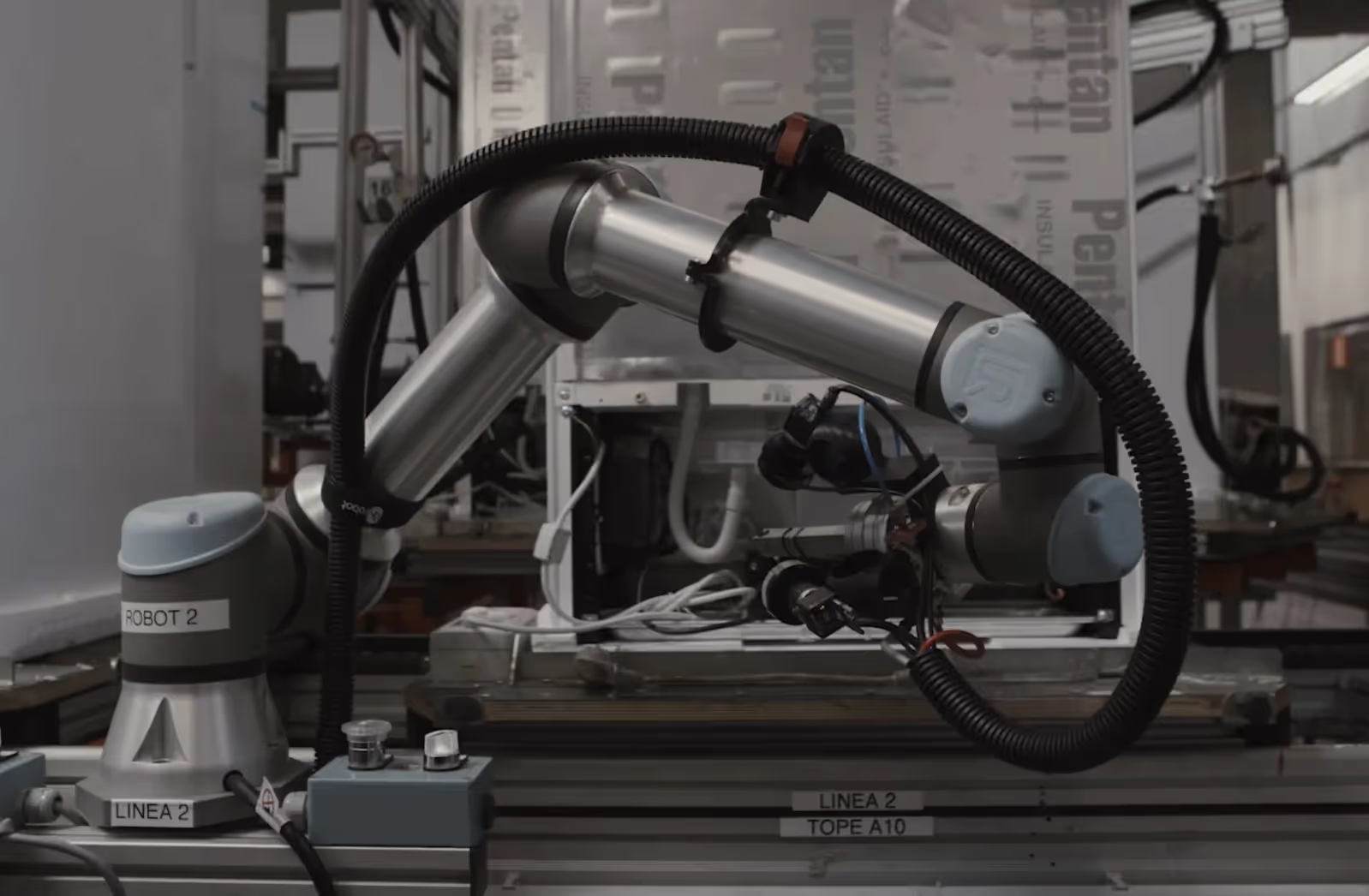
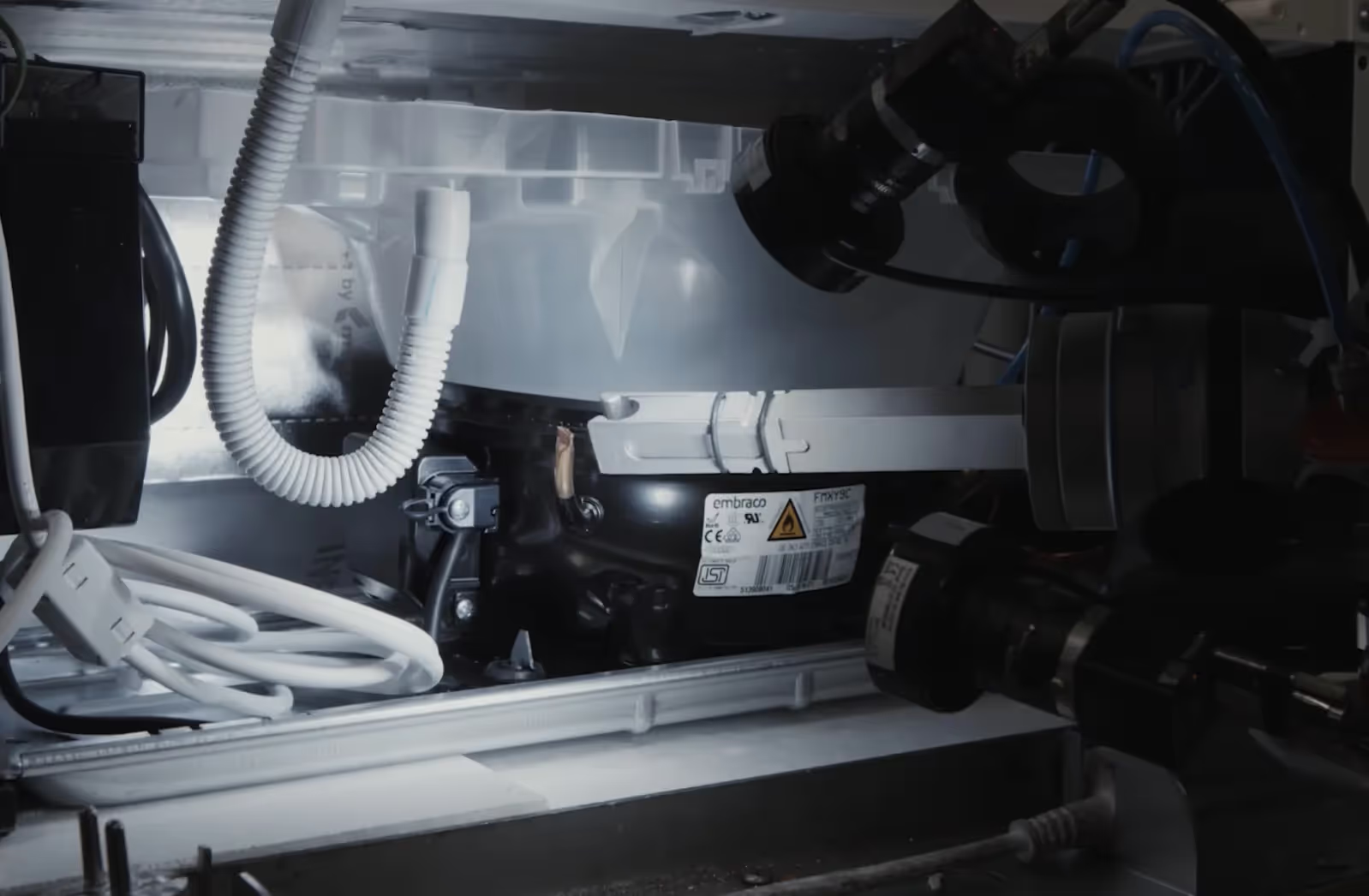
For that test, a sniffer probe is run along the solder points of pipes on the back of each refrigerator to check for leaking coolant. Since each pipe is manually assembled, crippled, or soldered, the measurement points vary in position, shape, and color. For traditional automation solutions, such variances present insurmountable obstacles. Therefore, the repetitive process is usually carried out by human workers.
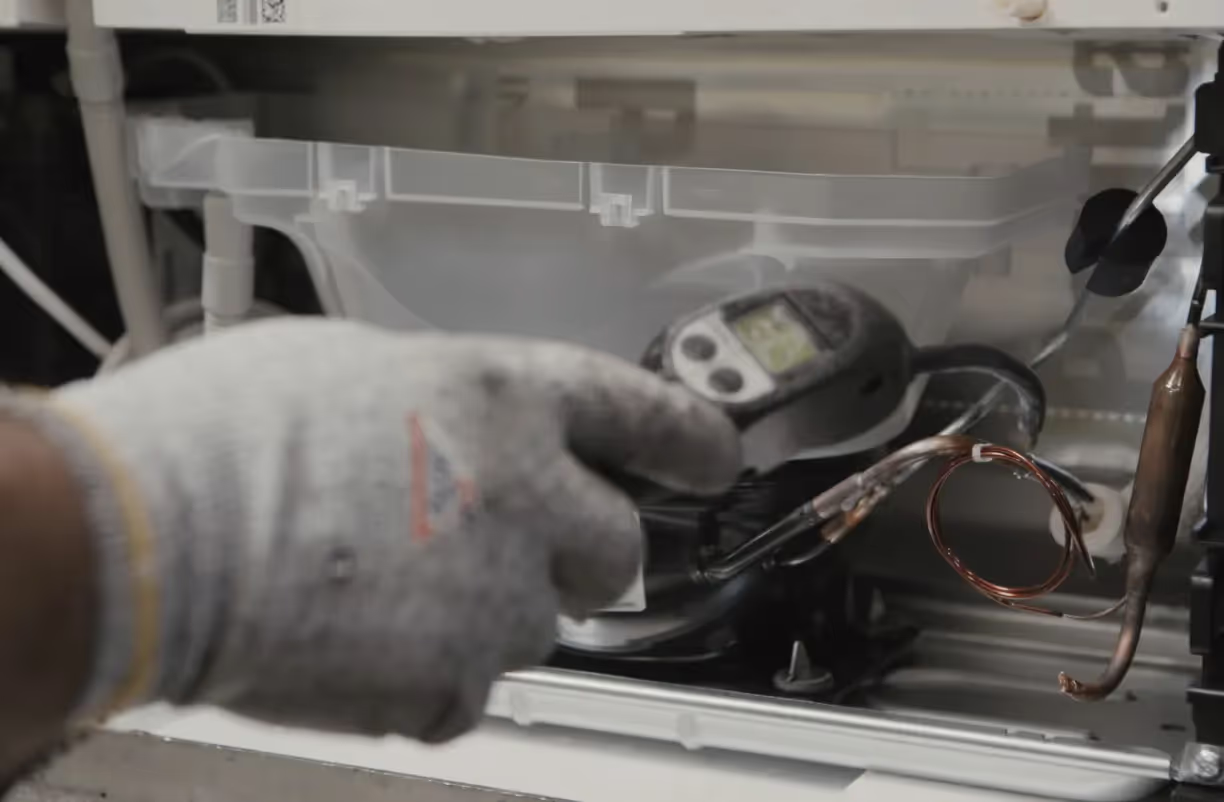
Market leader relies on AI for competitive edge
Micropsi Industries and BSH have successfully implemented a MIRAI-powered robot from Universal Robots in the leak testing task. Our AI-vision software enables the robot deployed at BSH to reliably identify all solder joints to be inspected and approach the sniffer probe with millimeter precision. This is made possible by MIRAI’s ability to respond to its environment in real time and to handle unforeseen variance.
Thanks to a customer success team at Micropsi Industries, BSH employees were able to train the MIRAI-equipped robot on the required skills in a few days, without the need for computer vision or AI expertise. Since the implementation of the MIRAI system, BSH has been able to reduce ongoing operating costs and maintenance and troubleshooting. The AI-vision solution is deployed in 24/6 serial production and offers high quality and absolute process reliability.
Using MIRAI, we have solved a challenge we could not solve with standard automation technologies. All cycle time, accuracy, and performance KPIs have been reached, improving productivity and quality.
Javier Chasco Echeverria, Engineer for Industry 4.0 at BSH, underscored the significance of machine learning technology for the industry-leading company: "We consider machine learning to be a key technology that we will continue using and will consider Micropsi Industries’ MIRAI for other challenging applications in the future."
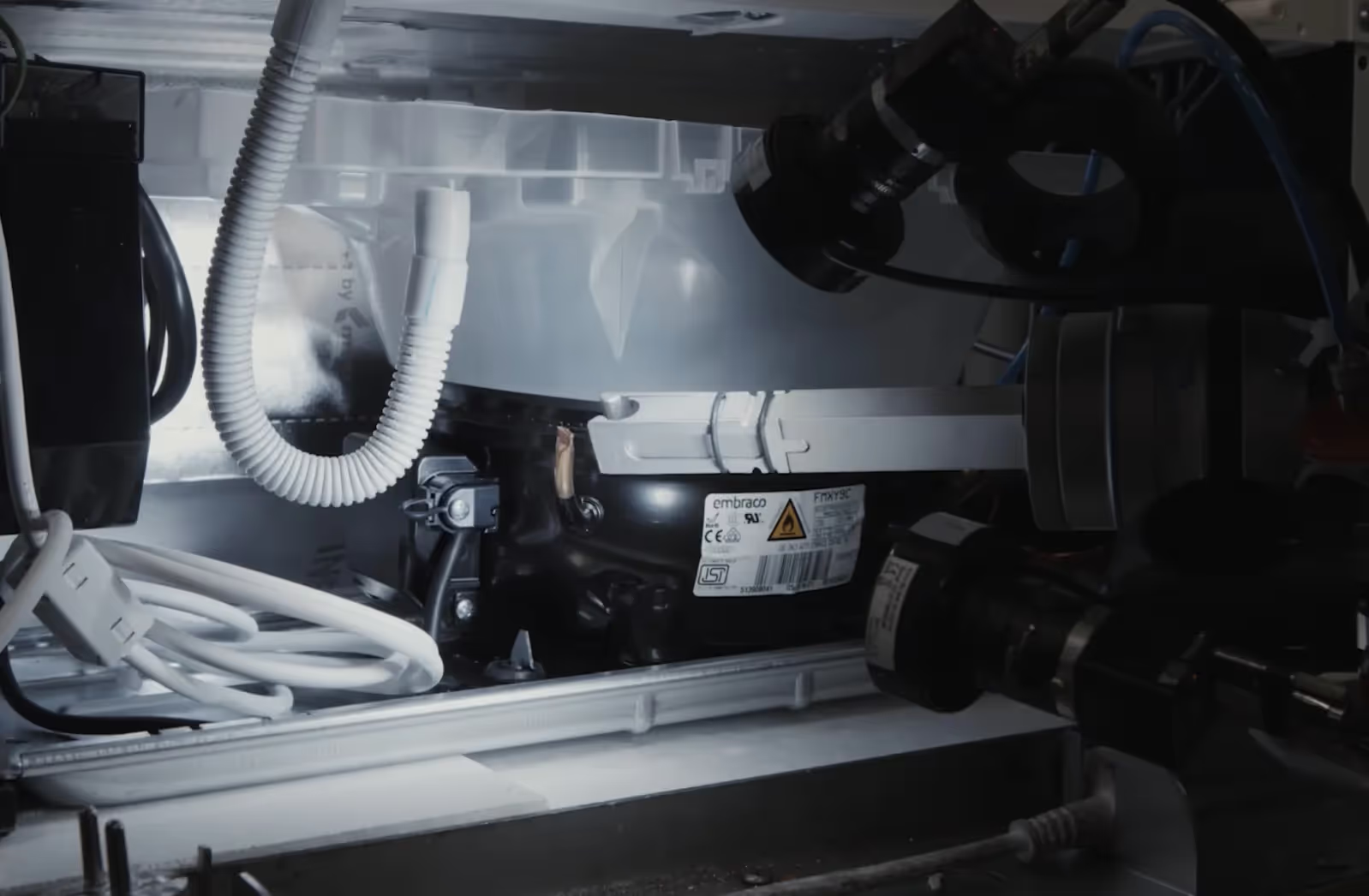
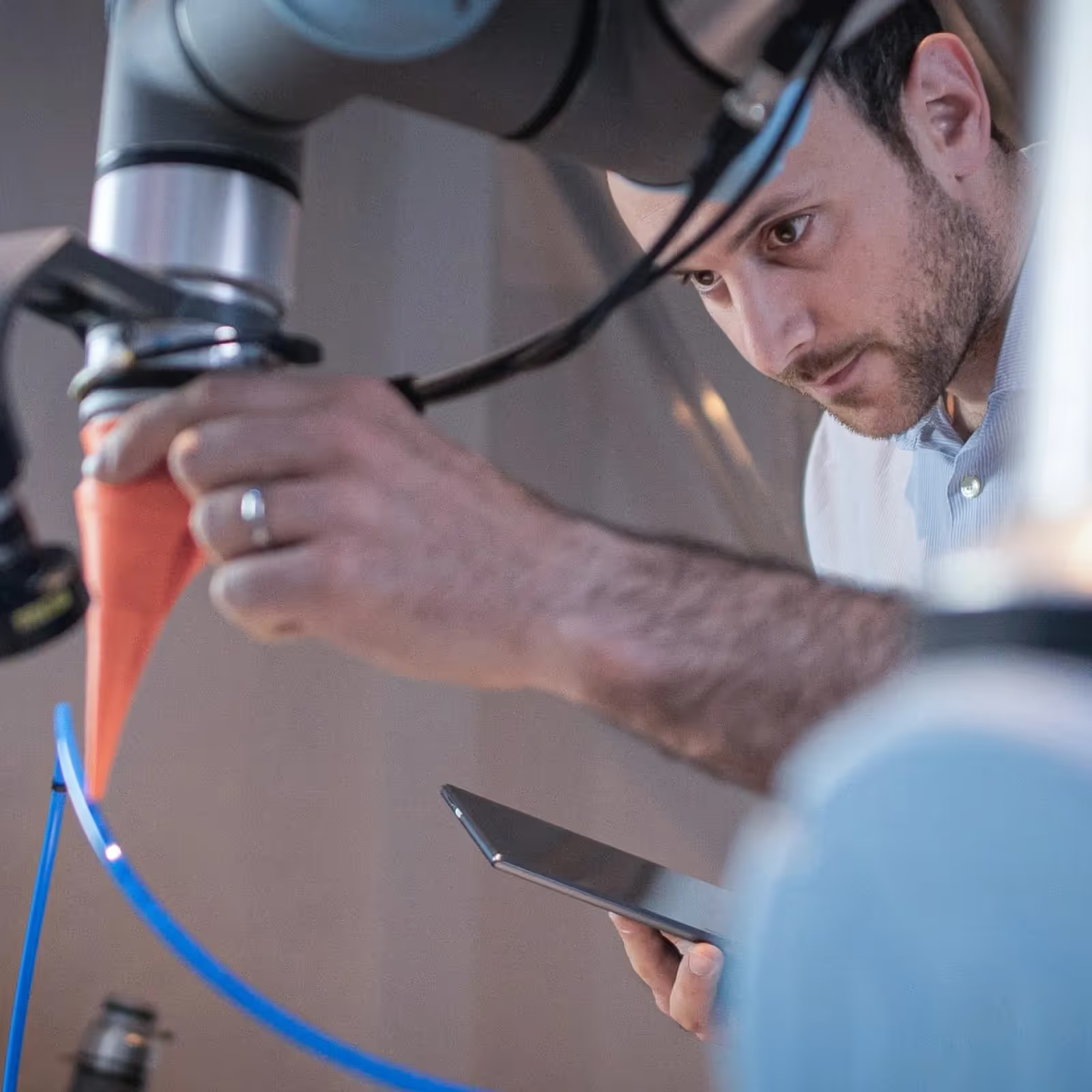
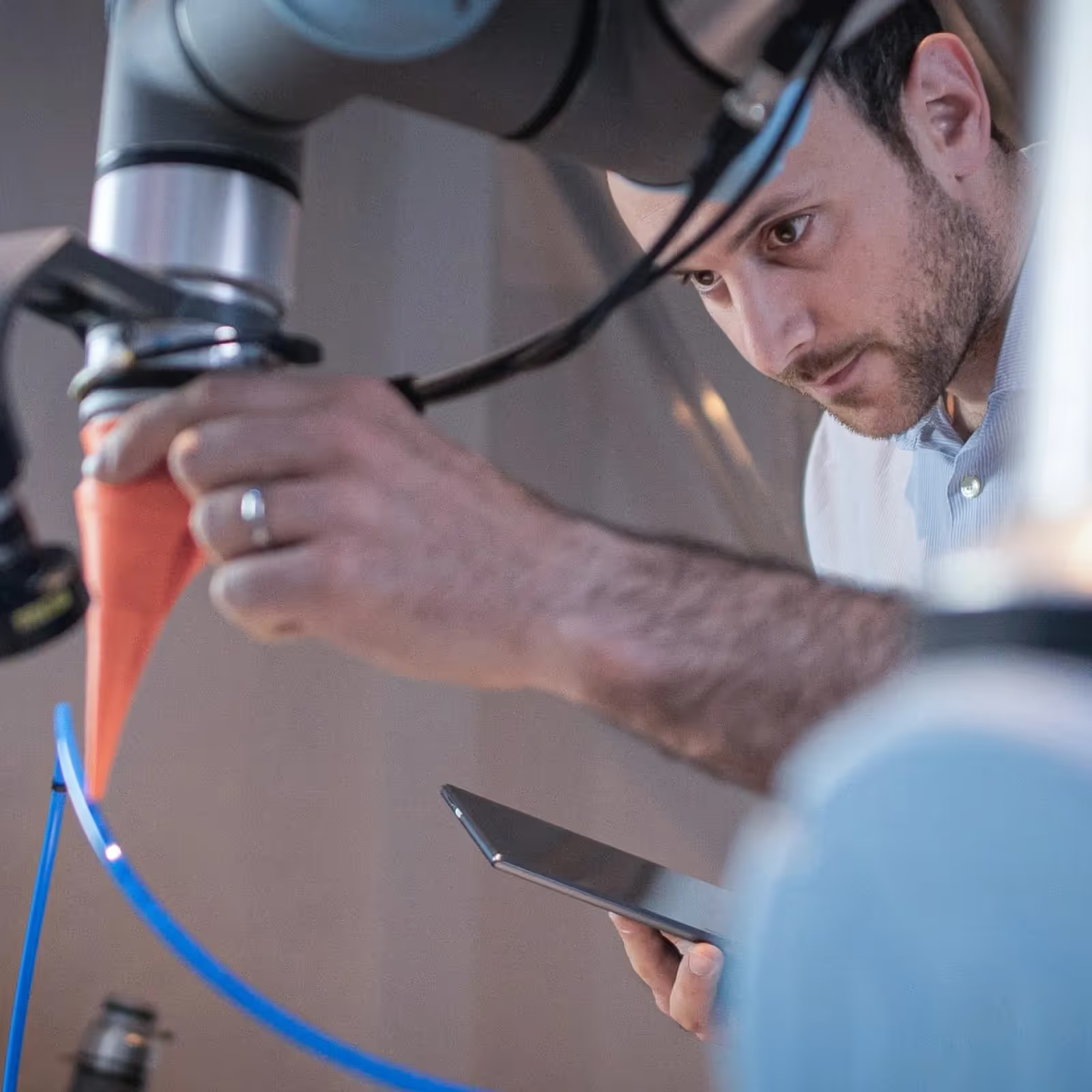