In our previous blog post, we explored the fundamentals of AI-powered machine vision and how it works. Today, we will further explore the applications of computer vision software in robotics and the significant benefits of integrating this advanced technology into various manufacturing processes.
What AI-powered machine vision brings to robotic automation
The integration of AI-powered vision in robotic automation is becoming a major milestone. These systems use sophisticated AI algorithms to analyze visual data in real time, overcoming variance in position, shape, color, lighting, and background. This capability allows robots to dynamically adjust their operations and perform tasks with a level of precision and flexibility previously only achievable by human operators.
AI-vision software plays a critical role in expanding the scope of automation, especially in scenarios characterized by irregularities and deviations in the work environment that traditionally require human intervention. While some tasks can be partially automated with standard vision systems today, their reliability often falls short. AI-vision software, on the other hand, excels at fully automating these complex applications.
Key applications of AI-computer vision software
As the manufacturing landscape becomes increasingly specialized, more robust systems for challenging tasks such as testing and assembling components are required. AI-powered computer vision software makes it possible to automate many of these applications that were previously performed by humans. Our AI-vision software, MIRAI, is particularly adept at automating tasks traditionally performed by humans, including:
- Cable insertion: Cable insertion requires precise manipulation and the ability to adapt to different connector orientations and positions, which can vary due to the slack and flexibility of cables. Conventional automation solutions lack the required dexterity and adaptive feedback mechanisms to handle such variance and ensure secure and accurate connections without causing damage to the cables or connectors.
- End-of-line testing: AI-powered robots can enable the automation of end-of-line tests, including leak testing and electrical safety tests. VDE testing is a standardized process that verifies the safety and quality of electrical devices and components before they leave the factory. During this process, testing probes are commonly used to evaluate product functionality and safety. To check for loose connections, the probe must be guided to specific points, such as the wires inside the device. Since these are not always positioned identically and differ in appearance, their locations cannot be defined by fixed coordinates.
- Screwdriving: Screwdriving and tightening processes in manufacturing can be challenging due to different screw positions, manufacturing tolerances or variances in the angle at which a screw needs to be tightened. Conventional automation systems are unable to compensate for these types of variance, which can lead to incorrect or inadequate fastening.
- Bolt torquing: Bolt torquing in manufacturing poses several challenges due to factors such as tolerance variations, material properties, surface conditions, and tool calibration and wear. These variances can impact the amount of torque required to achieve proper fastening, leading to issues such as under-torquing, over-torquing, uneven torque distribution, and torque angle deviation.
- Rack hanging: Hanging parts on racks for processes like painting or coating requires an understanding of part and hook orientation and the capability to continuously adapt to position changes. Traditional solutions lack the capability to adjust to varying shapes, sizes, and positions of hooks in real time, which is necessary for correct placement.
- Pick-and-Place: Many pick-and-place tasks are already automated today, but irregularly shaped, flexible, or inconsistently positioned items pose a challenge for traditional systems. These systems lack advanced vision to adjust to variances on-the-fly, which can result in mishandling, dropping, or damaging items. Furthermore, reflective or transparent pieces pose a challenge for traditional vision systems hard or impossible to overcome.
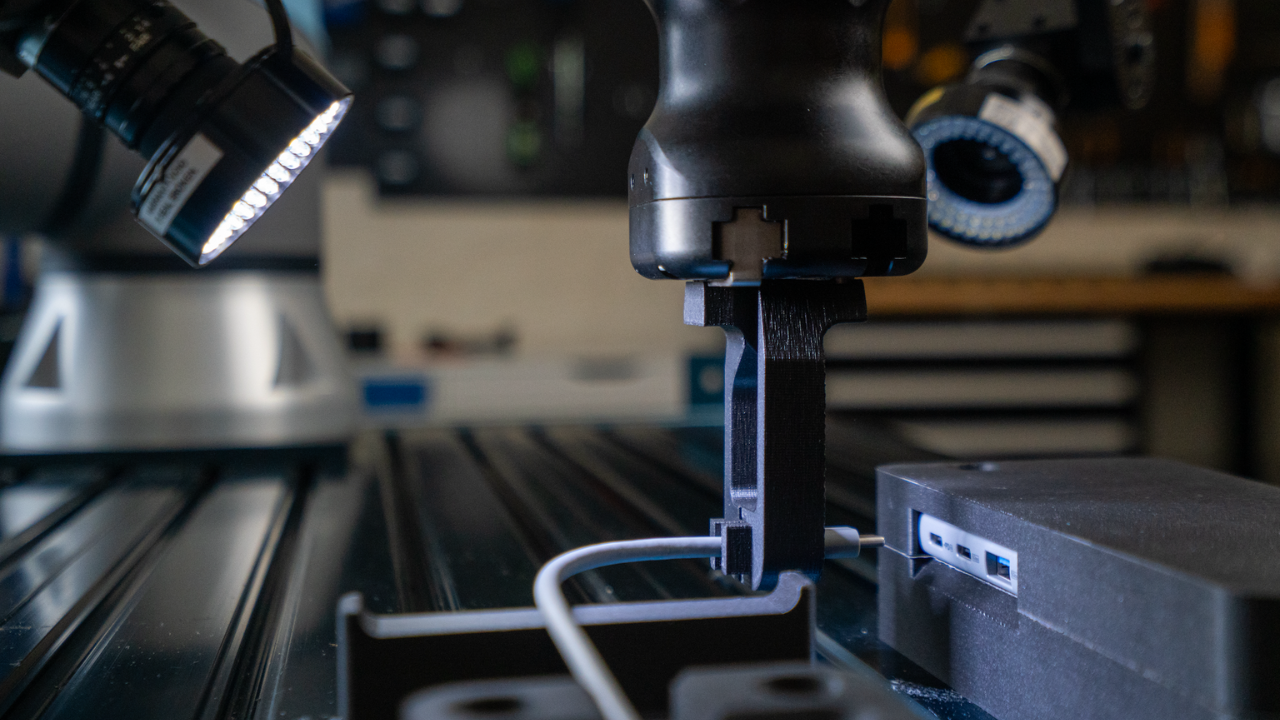
Cable insertion
AI-vision software can perform tasks that require both precision and adaptability, such as inserting cables.
Benefits of AI-vision software in robotic automation
AI-vision software significantly enhances operational efficiency and reduces costs by enabling the automation of tasks considered unfeasible. Here are some key benefits:
- Adaptability to variance: AI-vision software excels in environments where part presentation and conditions are inconsistent. It can adapt to unforeseen variance in position, shape, color, light or background in real time, ensuring that the process always remains stable and reliable.
- Increased efficiency and enhanced process stability: AI vision takes over where conventional solutions fail, and human workers are still needed. AI vision ensures that processes run 24/7, even when labor shortages occur, and helps achieve consistent production output.
- Precision and accuracy: AI-vision software can identify and align target objects with high precision, regardless of variance. This is critical for tasks that require millimeter-level accuracy, such as positioning a sniffer probe or inserting a needle into tiny holes.
- Reduction in operational costs: The automation of complex tasks reduces the need for manual labor, which can lower ongoing operating expenses. Additionally, maintenance and troubleshooting demands are often reduced, contributing further to cost savings.
- Filling work gaps and improved ergonomics: AI-vision software enables the automation of tasks that were previously handled manually, effectively addressing labor gaps and reducing the physical strain on workers. This shift not only fills workforce shortages but also enhances ergonomic conditions by eliminating the need for human workers to perform repetitive, strenuous, or precision-critical tasks.
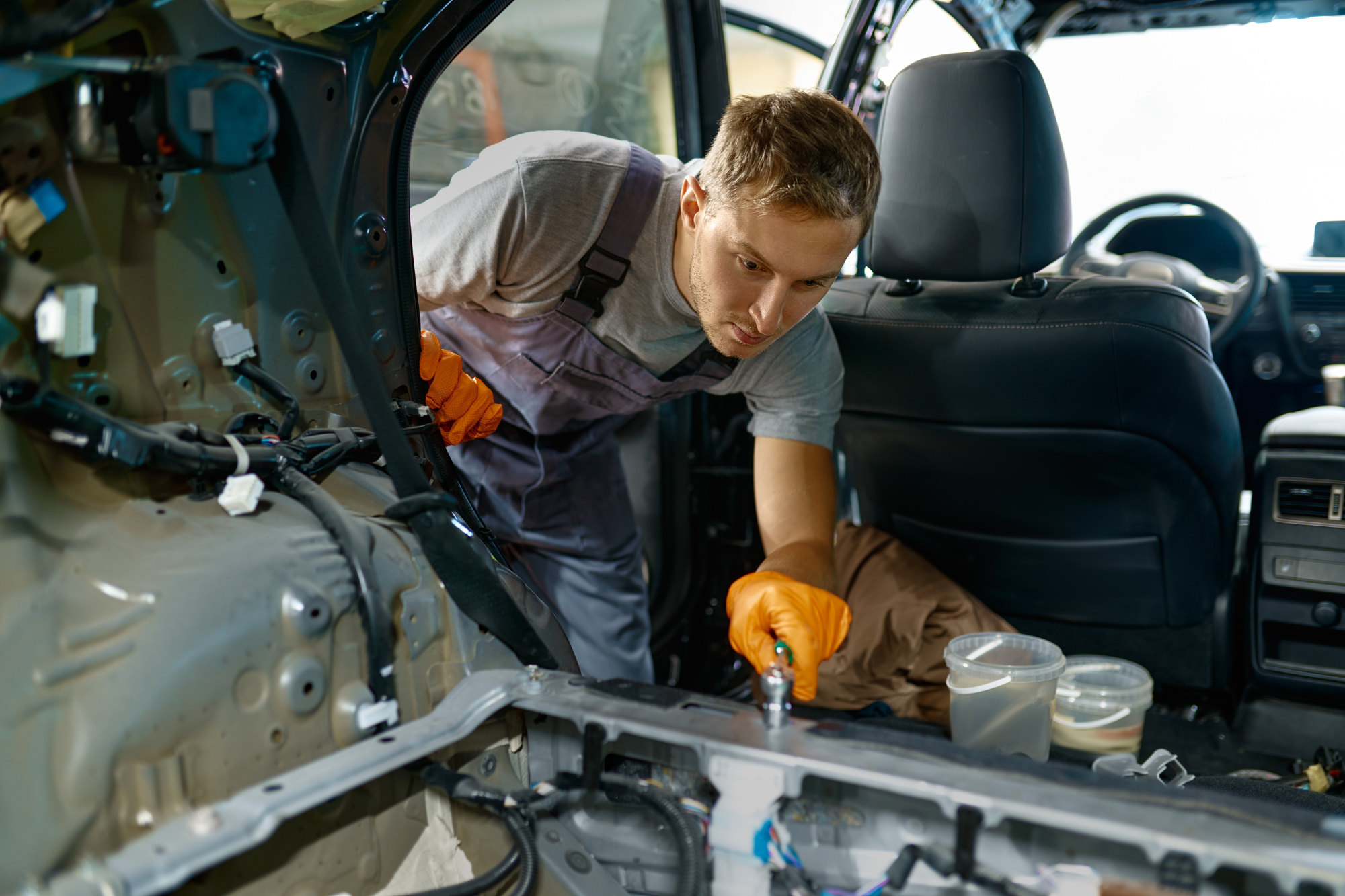
Wrench torquing
AI-powered robots not only relieve employees of non-ergonomic tasks, but also fill gaps in the workforce.
The integration of AI-powered machine vision into robotic systems is solving manufacturing challenges that were previously insurmountable and setting new standards for quality and reliability in production processes. As manufacturing demands evolve, higher accuracy and productivity are required, and labor is scarce, the strategic importance of investing in AI-vision software becomes clear. For companies that want to be leaders in their markets, adopting this technology is critical to remaining competitive and profitable.
Want to learn more about MIRAI, our AI-vision software? Watch the free demo video.